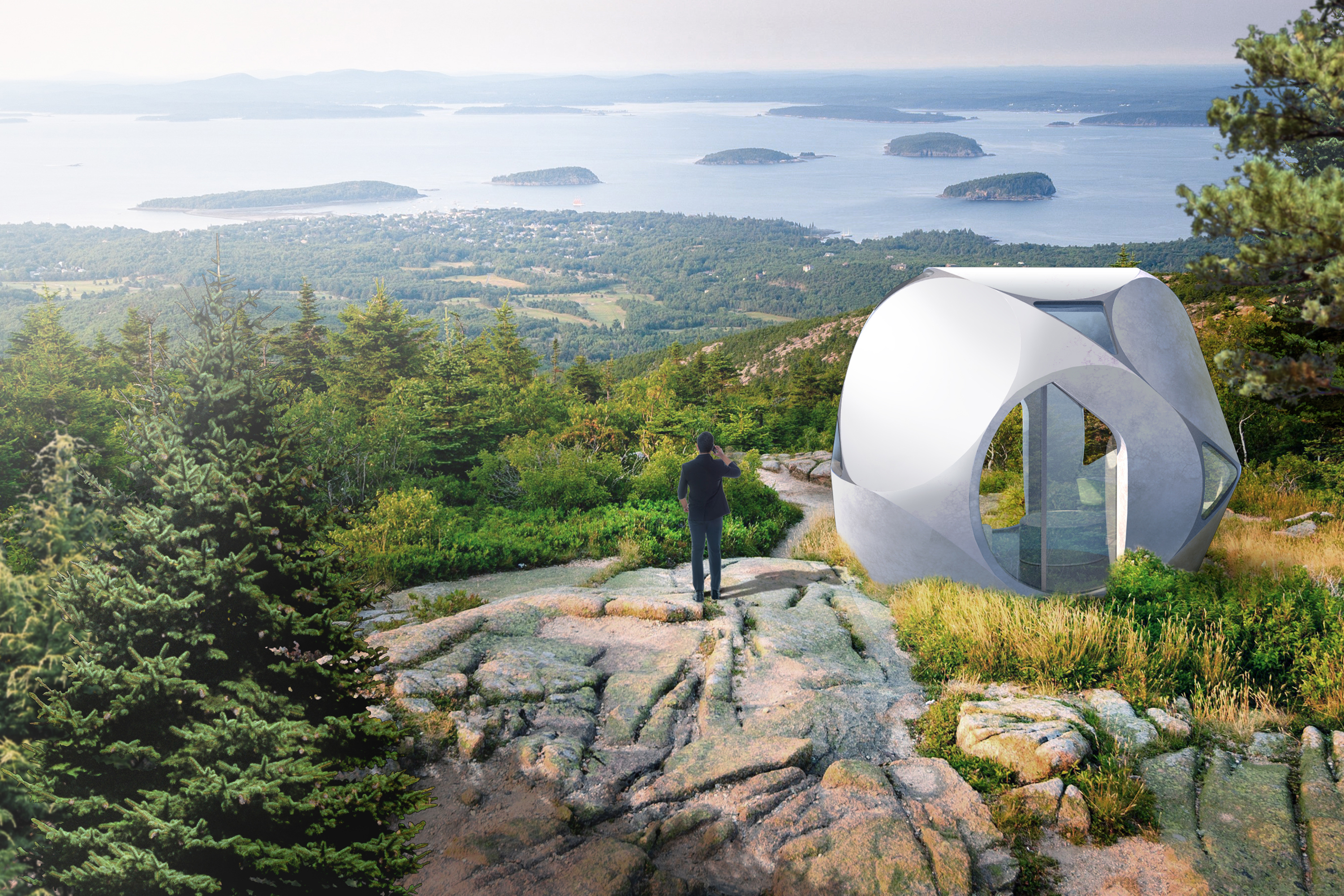
Sphere set on mountaintop overlooking ocean
Serendix Sphere is an advanced housing prototype that employs in situ 3D-printing technology to quickly and economically fabricate small residences. The design is a progression of our interest in habitats for extreme environments, and builds on the success of the award winning Mars Ice House concept prepared for NASA.
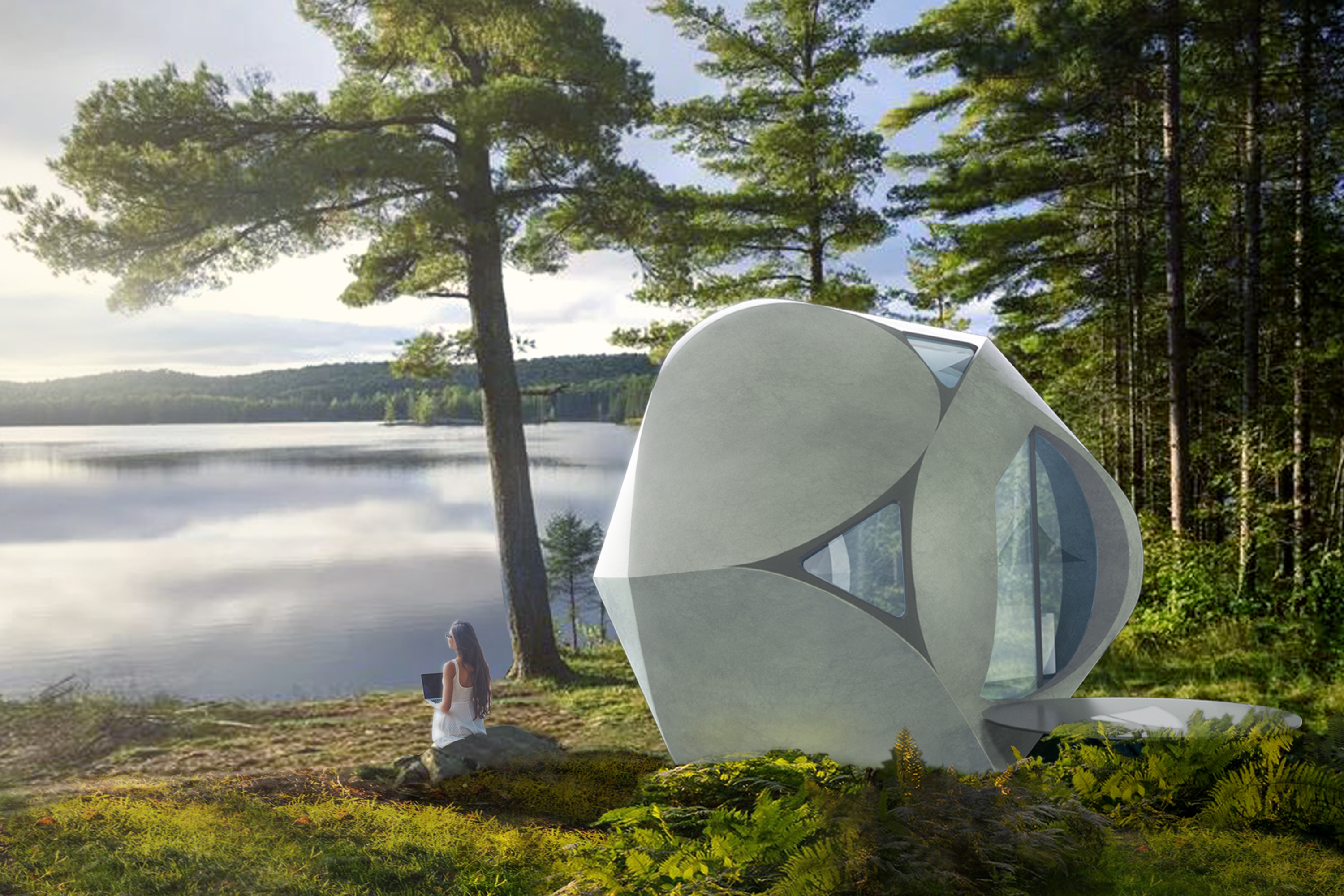
‘Glamping’ unit deployed lakeside for a productive retreat
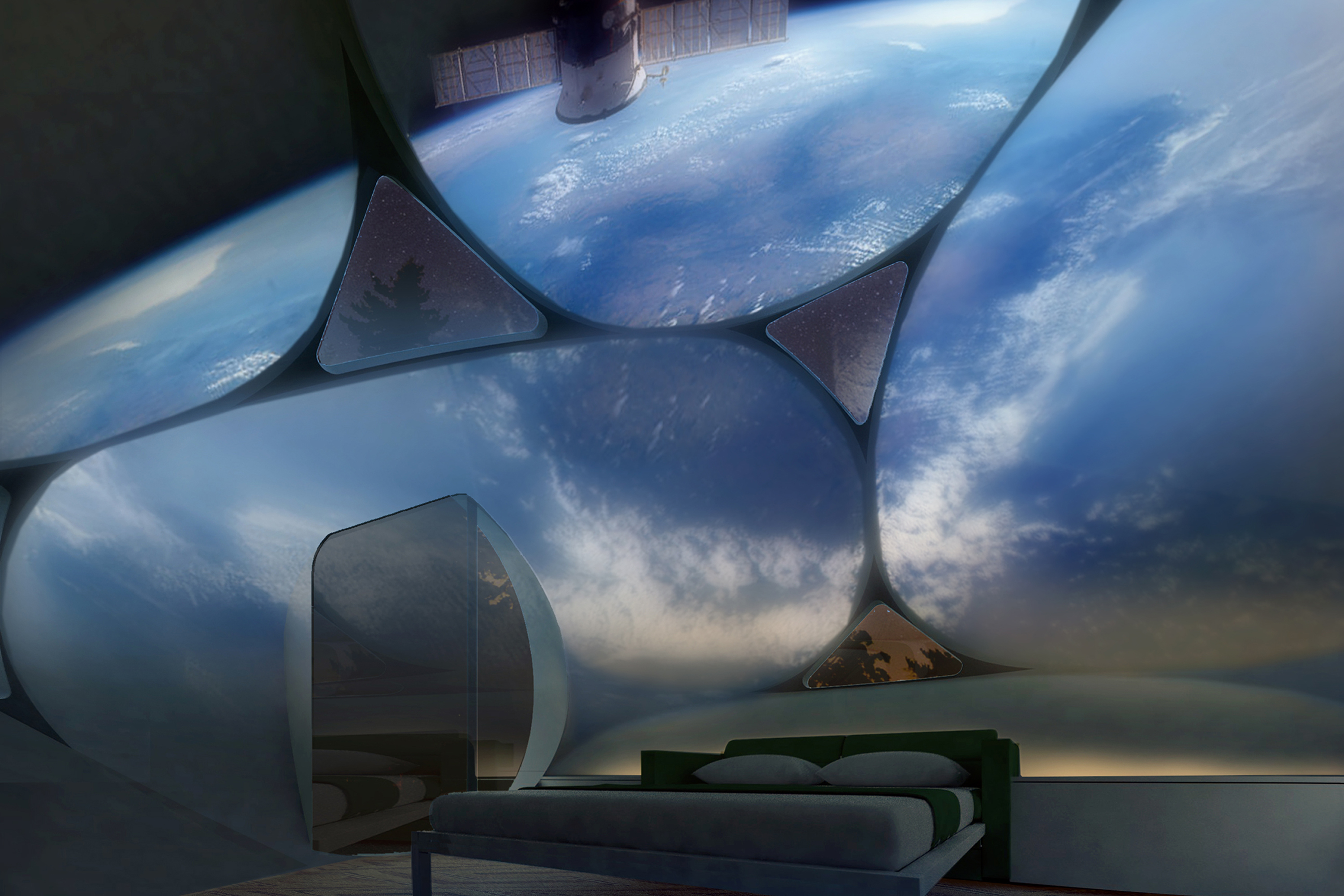
Interior of unit at night with projection mapped video
Digital additive manufacturing allows for cost effective variations and flexibility by streamlining the fabrication process, minimizing labor and material transportation. With its swift production and structural capacity, it is also envisioned to serve as emergency shelters in an event of a natural disasters which have been increasing globally in recent decades.
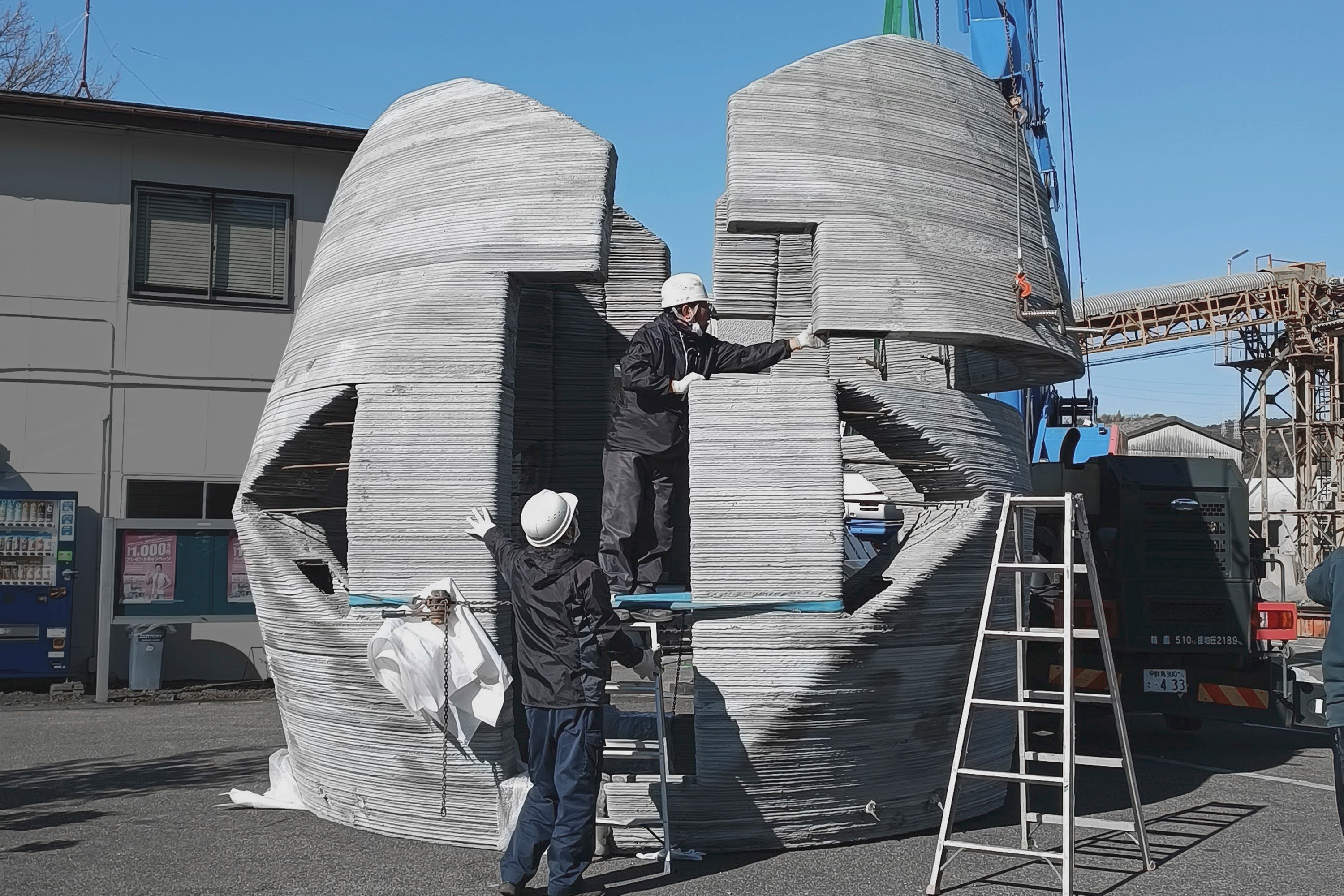
Assembly of the 3D-printed parts ( © Serendix )
Sphere is a form that has the largest surface area to volume ratio and structural high stability. It also has versatility that can fit in diverse site conditions and orientations. Serendix Sphere, designed by Clouds Architecture Office is aimed to create smart, durable and sustainable dwelling prototype by expanding the potential of additive manufacturing technology in design and construction.
Sphere is composed of twelve identical base segments trimmed from a cylinder. The resulting volume has a unique geometric property that its shape changes from round, hexagonal to softened square depending on vantage points. This creates a dynamic effect as if it is constantly changing its profile as people walk around the structure. When multiple units are installed in a cluster such as in case of cottage or camping ground, this provides diversity and avoids the Next House from looking monotonous while maintaining a consistent design vocabulary.

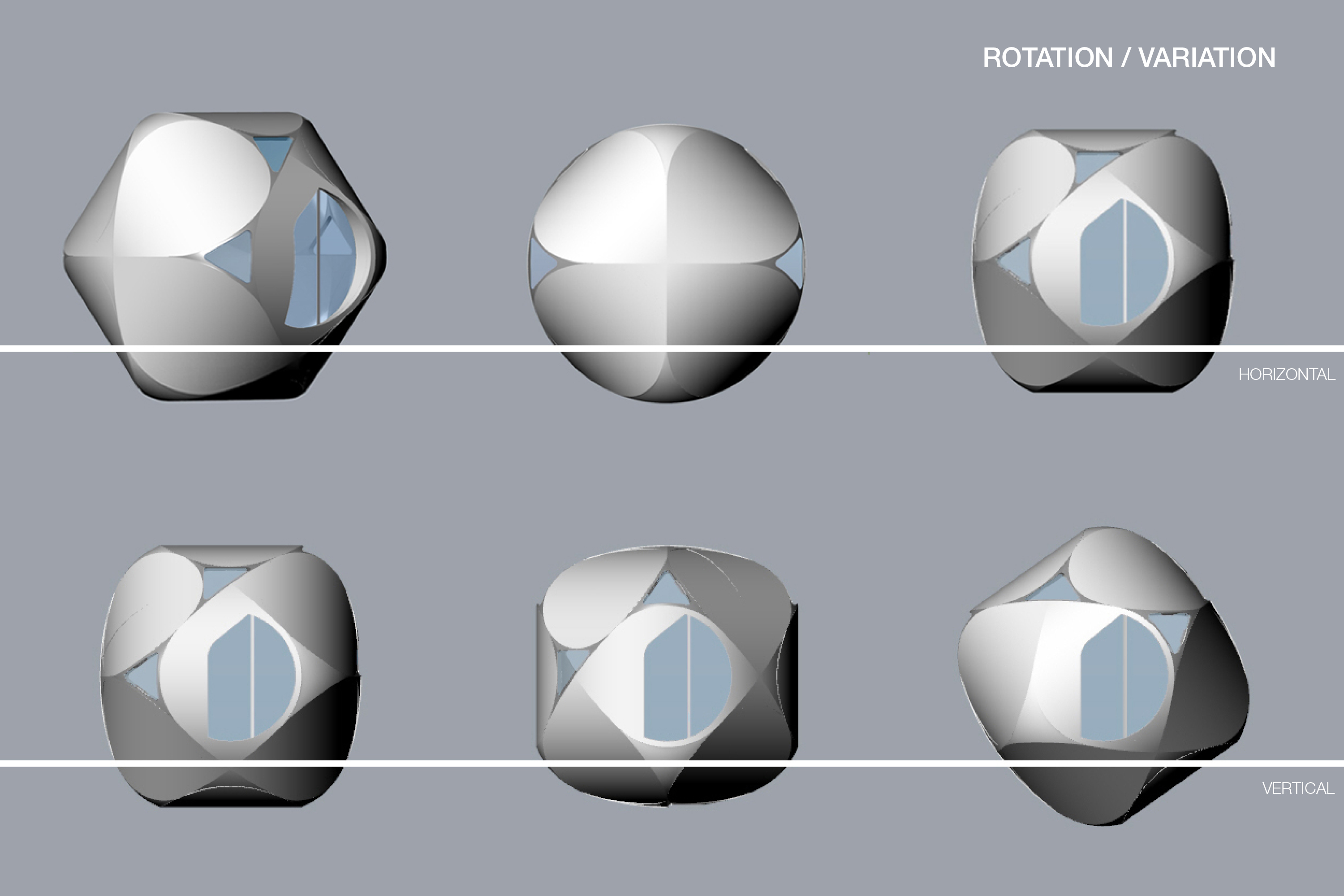


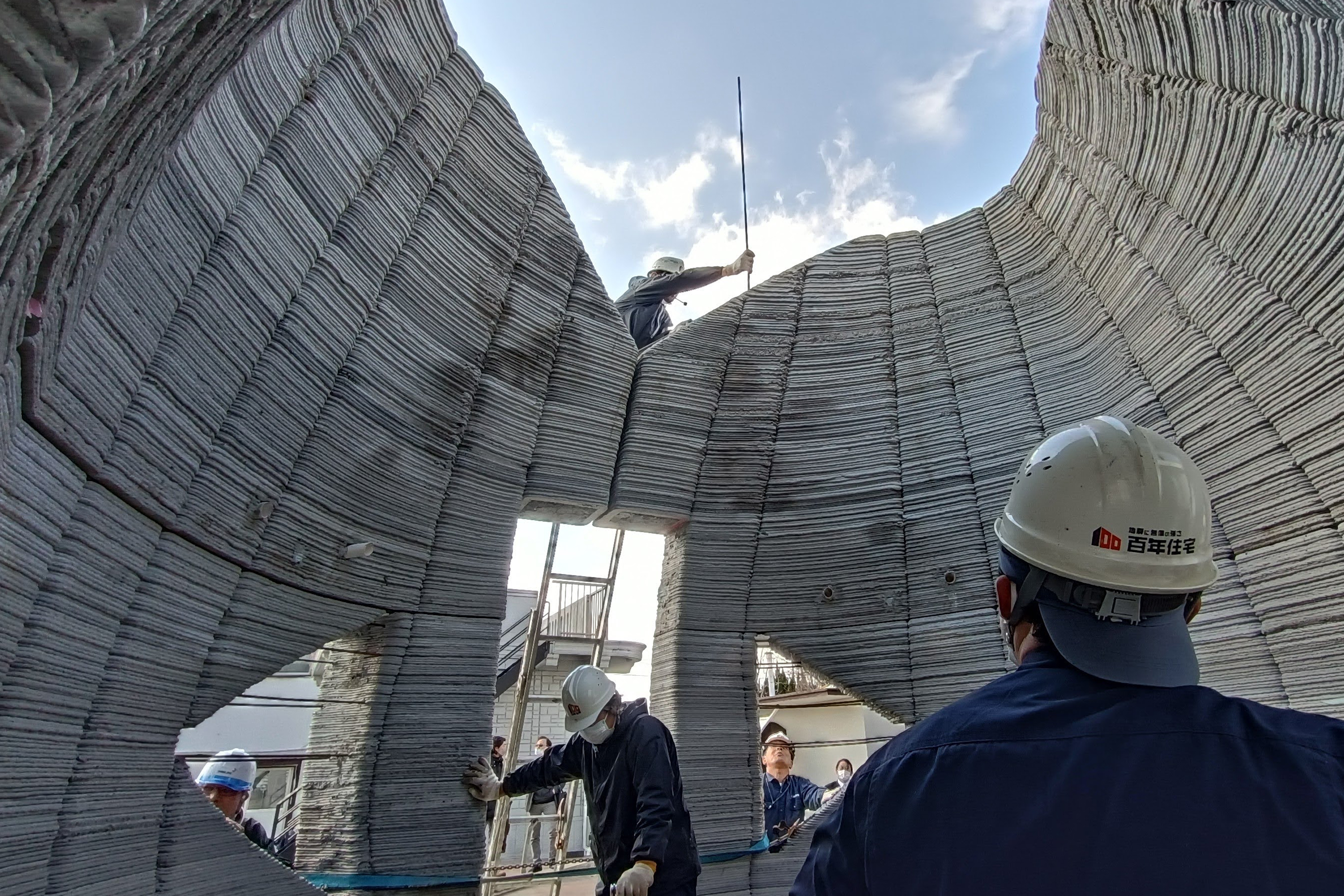
Formal concept diagram, variations, parts assembly, 3D-printing and assembly
By taking full advantage of customization capacity of 3D printing, window locations can be flexibly adjusted and even the entire base model can be rotated in vertical orientation to achieve variations in design and form (such as vault, dome and pitched roof profiles) to satisfy customer preferences, use and site conditions. Multiple units can also be connected and expand to house larger programs and floor areas. Viewed from the interior, curving walls create an immersive spherical projection setting to form multimedia screen.
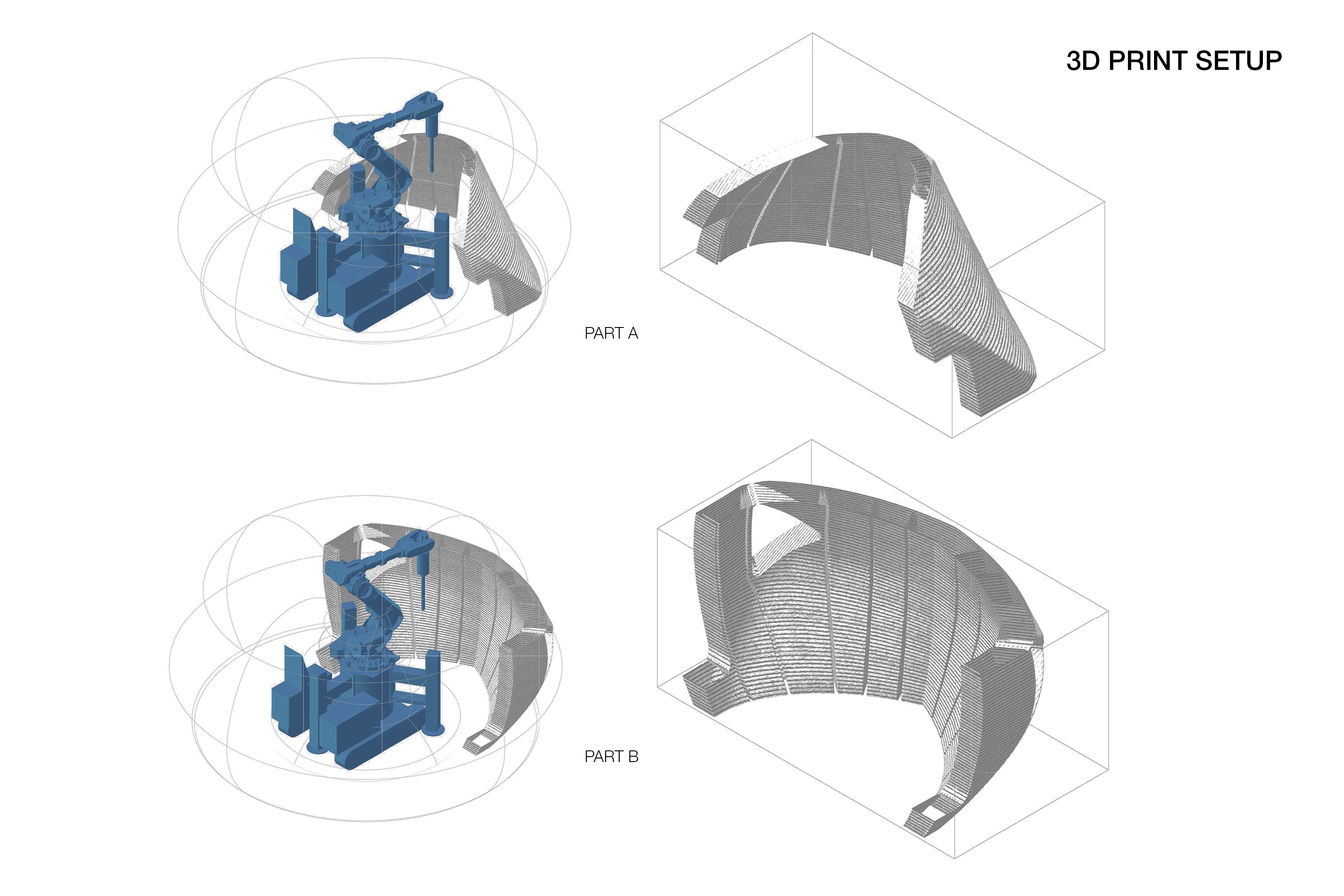
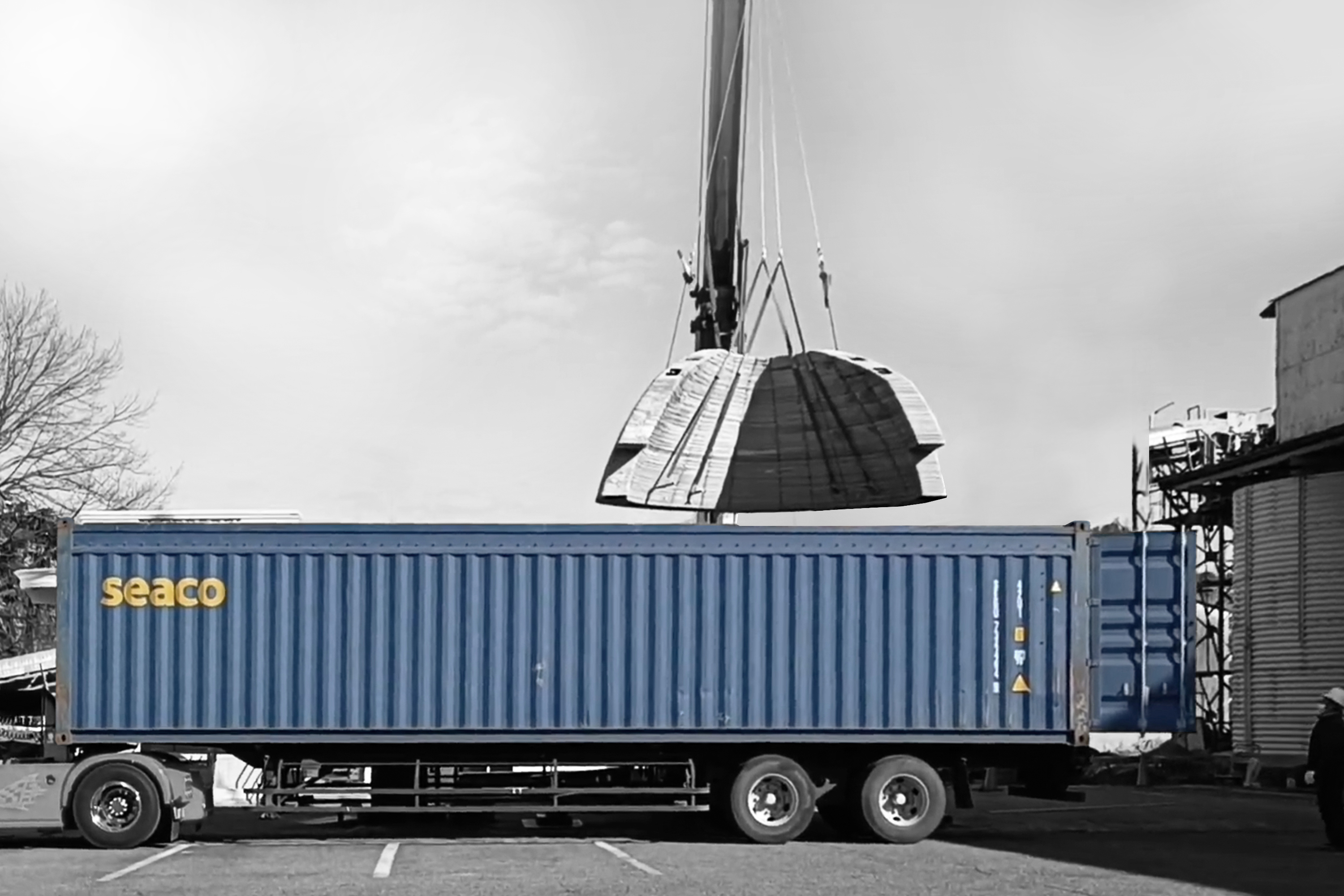
3D-printing parts setup for container transport


Full scale mock-up
The goal is to print each unit on site for highest efficiency. Due to identical base geometry of all members it can also be pre-printed in controlled factory environment and assembled on site in case the site condition limits use of in situ printing. First full scale prototypes have been printed on two different continents and a proof-of-concept unit has been assembled in Japan. The fabrication process is planned to be further developed and upgraded for coming prototypes.
Location: Worldwide (based in Komaki, Aichi, Japan)
Completion Date: March 2022
Owner: Serendix Inc
Design: Clouds Architecture Office
Structural Consultant: Chihiro Katoh
Assembly and Constrution: Hyakunen Jutaku Co Ltd, Kaede Koumuten, Nabejyu Co Ltd